This story is co-authored by Dylan Romero (Makers Lab), Moniqua Crawford (First Impressions), and Khary Dvorak-Ewell (First Impressions)
Introduction
Over the past six years more UCSF community members have incorporated 3D printing in their education, teaching, and research. As the community discovers more applications for 3D printing in the health sciences, it is critical to remain conscious of our environmental footprint. This has been a priority for the UCSF Library’s Makers Lab even before publishing the Closing the Loop on 3D Printing news story in 2017. Supporting solutions for reducing our environmental impact, such as recycling 3D printed waste, is not a simple task. It would not be possible to operationalize these efforts if it were not for the following partnerships developed with other UCSF departments.
Partnerships
The Makers Lab has saved its 3D printed waste since 2016. In 2019, the Makers Lab purchased an industrial filament shredder to break down 3D printed waste into smaller granulates. In 2020, the Makers Lab partnered with the UCSF Office of Sustainability to purchase a filament extruder used to melt and extrude the granulate into usable 3D printing filament. This helped bring us one step closer to a closed loop system for 3D printing at UCSF. The UCSF Office of Sustainability has also provided recommendations for other types of plastics that the Makers Lab may be able to recycle and use for 3D printing.
In 2020 the Makers Lab began to collaborate with the First Impressions Program, part of UCSF’s Citywide Case Management, to offer 3D printing workshops for the program’s trainees. First Impressions is funded by San Francisco’s Mental Health Service Act (Prop. 63), and provides a paid 6-month on-the-job training program for local residents receiving mental health services. It offers job training in mechanical and machine maintenance through 3D printing, as well as customized training for jobs in home improvement stores and the emerging 3D printing industry. There were some immediate synergies that came out of the First Impressions and Makers Lab partnership, one of which was recycling 3D printed waste. In March 2022, the Makers Lab loaned the industrial filament shredder to First Impressions and together they created a new job opportunity for First Impressions’ graduates.
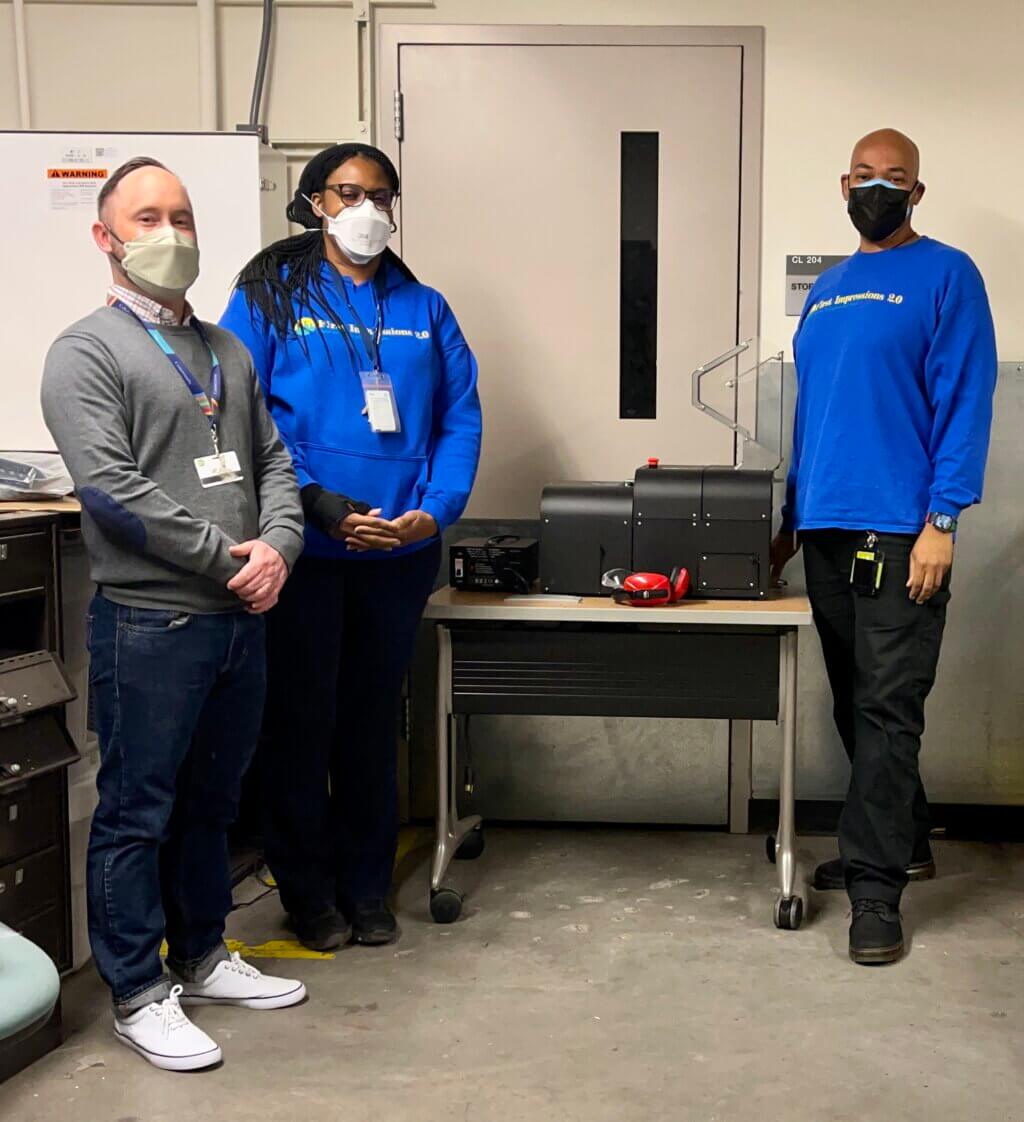
Filament recycling process
It will be helpful to revisit the lifecycle of 3D printing filament. Filament is the thermoplastic feed-stock used in the fused deposition modeling (FDM) 3D printers used in the Makers Lab, First Impressions, and other UCSF locations. There are many types of thermoplastics that are used to make filament, the most common used by the Makers Lab is polylactic acid (PLA). FDM 3D printers push the filament through a heated extruder, melting it so it is laid down layer-by-layer onto the print bed. The process repeats, with the plastic cooling and setting each time, binding each layer together to create the desired three-dimensional model.
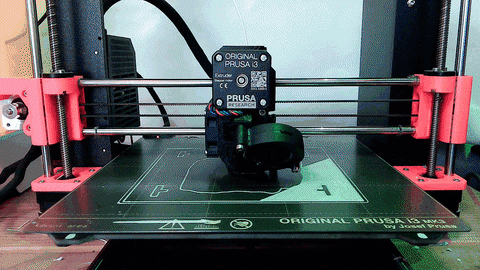
What is 3D printed waste? 3D printed models often rely on support structure to reinforce the model to prevent sagging while printing. Support structure is removed and discarded after the 3D print has finished, resulting in waste that cannot be recycled or composted in most facilities and often ends up in landfills. Additionally, there is not a 100% success rate and 3D prints will sometimes fail, resulting in additional 3D printed waste.
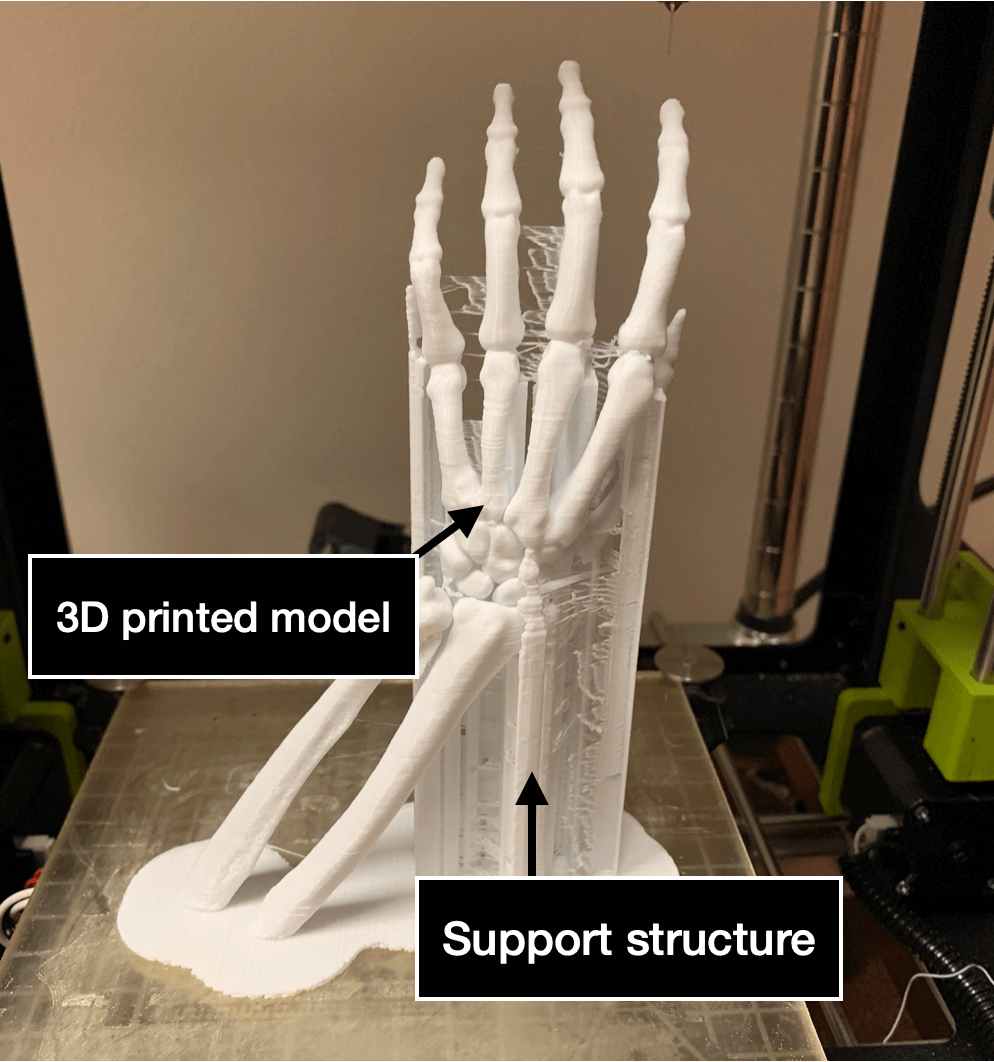
How are the Makers Lab, First Impressions, and Office of Sustainability partnering to create a sustainable 3D printing ecosystem at UCSF? First, all 3D printed waste is saved by both the Makers Lab and First Impressions. For example, the Makers Lab uses an average of 10 kilograms of filament in a month and we estimate that 10% results in 3D printed waste. That is 1,000 grams (or over 2 pounds) of plastic per month that would otherwise end up in landfills just from the Makers Lab! Additionally, First Impressions uses an average of 1 kilogram of filament each month and estimates 5% of that turns into 3D printed waste.
First Impressions collects 3D printed waste from the UCSF Library and brings it to their training warehouse in San Francisco. First Impressions trainees sort the filament by color and shreds the filament into granulate.
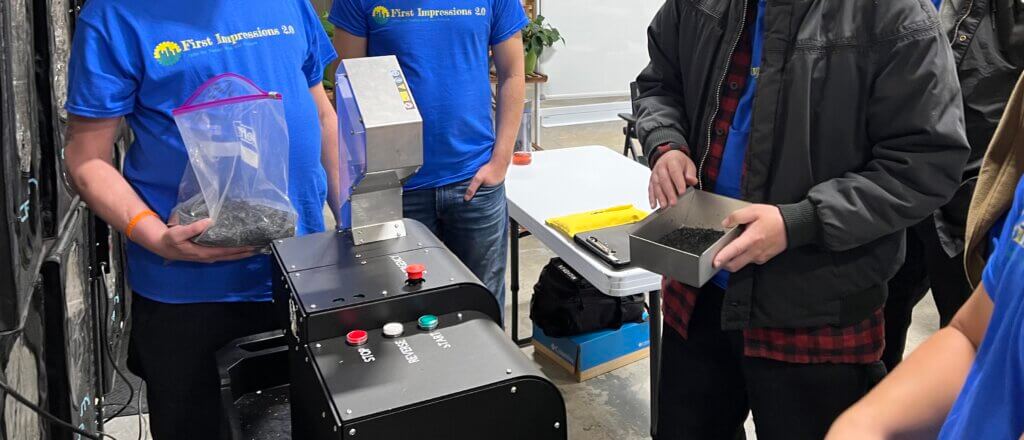
First Impressions staff bring the granulate back to the UCSF Library where it is extruded into usable 3D printing filament. The extruder can accept a mixture of shredded PLA granulate and raw PLA pellets. While adding raw PLA pellets helps produce more reliable filament, our goal is to produce 100% recycled, usable, filament to support 3D printed health sciences projects.
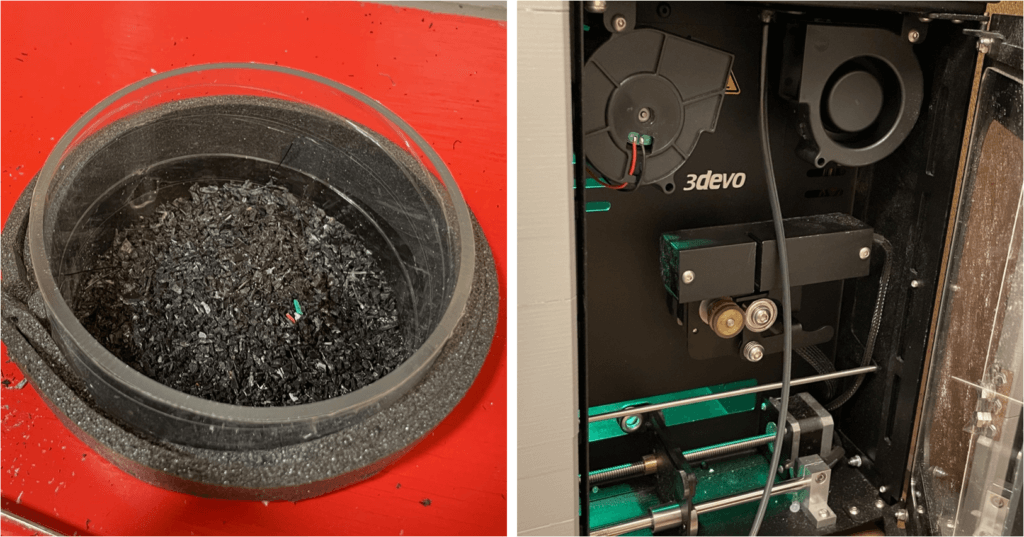
Next steps
While recycling 3D printed waste is helping to reduce our environmental footprint, we have identified the following challenges and opportunities.
Accepting 3D printed waste
We are not ready to accept 3D printed waste from the larger community at this time. Currently, only 3D printed waste from the Makers Lab and First Impressions is being recycled. This is because extruding 3D printed waste with different material properties presents challenges. Filament has different melting temperatures, even for the same types of thermoplastics (e.g., PLA) made by different manufacturers. This can lead to unreliable recycled filament due to inconsistent filament diameter. Because the Makers Lab and First Impressions each use one type of filament respectively, we can avoid mixing filament with different material properties when recycling. We look forward to gaining more experience with the recycling process and eventually set up bins to collect 3D printed waste from 3D printing enthusiasts at UCSF and across the Bay Area.
Strategically minimizing filament
It is important to minimize the amount of filament used before 3D printing a model. This is achieved through strategic 3D design to minimize support structure and infill. This strategy results in 3D printed models that have the same appearance and functionality, but use less filament. The Makers Lab offers training and consultations on strategic 3D modeling and printing for the First Impressions Program and the entire UCSF community to help minimize filament waste.
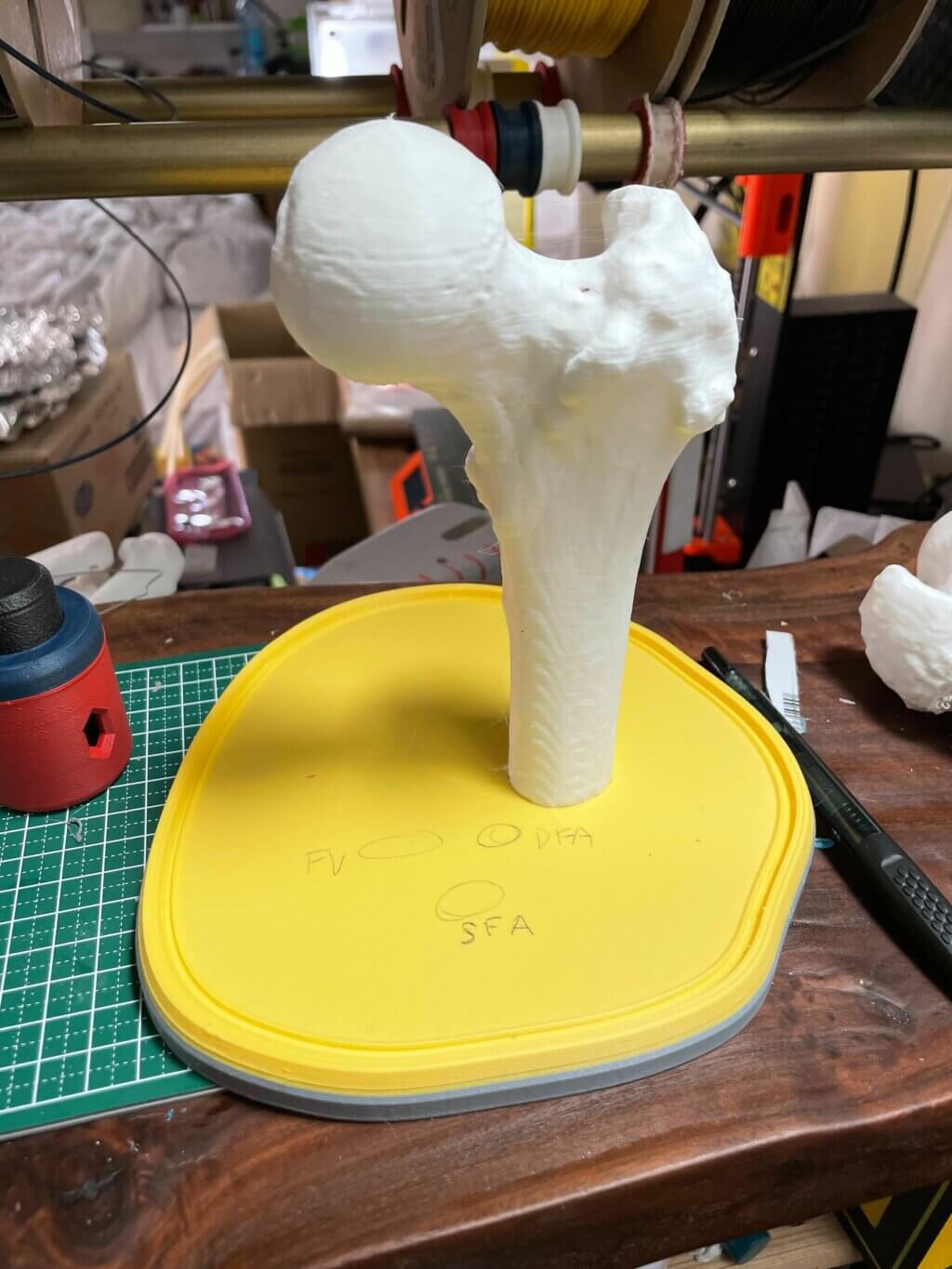
Purchasing environmentally-friendly filament
The Makers Lab uses the most environmentally-friendly filament available. While we strive to recycle as much 3D printed waste as possible, it is inevitable that some waste will not be recycled. For example, when someone 3D prints a model in the Makers Lab, that model may eventually be tossed in the trash. The Makers Lab is currently 3D printing with Polymaker PolyTerra PLA. PolyTerra PLA degrades around 93.6% after 45 days, while standard PLA degrades around 79.9% in the same amount of time (Polymaker.com). PolyTerra packaging and spools are made from recycled materials and is 100% biodegradable. Additionally, for every spool of PolyTerra PLA that is purchased a tree is planted where the spools are sold in partnership with One Tree Planted Association. First Impressions is also transitioning to using PolyTerra PLA. We are always looking for environmentally-friendly filament, so please send us your recommendations!
Experimenting with the lifespan of recycled filament
Research has been published on how many times filament can be recycled before it becomes unusable. The research shows that “unless done perfectly, there’s a noticeable loss of performance in re-extruded filament. Its tensile strength is reduced from around 40 to 35 MPa, which is enough to create a much higher chance of breakage while being extruded by your 3D printer. It also means a higher chance of warping, which can push your whole object out of shape” (All3DP.com, 2021).
First Impressions and the Makers Lab are researching how many times they can recycle filament before it becomes unusable. Even if the filament can only be recycled a few times, it still reduces the environmental impact and generates cost-savings due to fewer filament purchases.
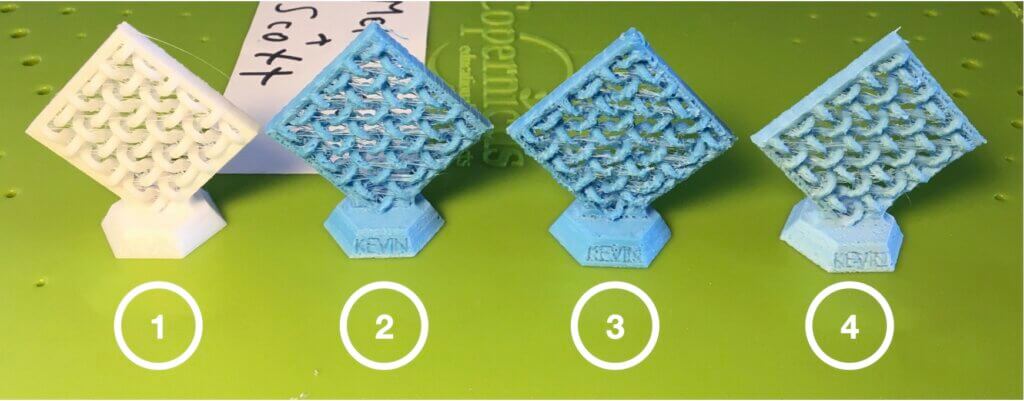
Recycling other plastics for 3D printing
The UCSF Office of Sustainability has identified a number of other types of plastics used at UCSF that cannot be recycled at most recycling facilities because the items have been used in research. These include, but are not limited to, polypropylene (PP) and high-density polyethylene (HDPE). As we become more experienced with the recycling process, we look forward to experimenting with recycling and 3D printing different types of plastics commonly used in UCSF research. We will need to ensure that these and all types of plastics are extruded in a well-ventilated and safe location due to potential off-gassing.
Identifying other applications for 3D printed waste
3D printing is not the only application for recycled 3D printed waste! We are interested in hearing your ideas for ways we can repurpose 3D printed waste to support the mission of UCSF. One idea is to melt the granulate in large trays to create sheets of PLA. This could potentially be used with the laser cutter or CNC machine in the Makers Lab.
We hope you follow us as we work together to make 3D printing more sustainable. Contact the Makers Lab if you have any questions or suggestions for the recycling process.
Resources
- All3DP. (2022, August 19). 3D Printer Filament Recycler: All You Need to Know. https://all3dp.com/2/the-3d-printer-filament-recycler-s-guide/
- All3DP. (2021, July 20). Is PLA Recyclable? – Simply Answered. https://all3dp.com/2/is-pla-recyclable/
- All3DP. (2021, July 24). PLA Plastic / Material – The Ultimate Guide. https://all3dp.com/2/what-is-pla-plastic-material-properties/
- Polymaker. PolyTerra Infographic Degradability. https://cdn.shopify.com/s/files/1/0548/7299/7945/files/Polyterra_Infographic_Degradability.pdf?v=1641022985